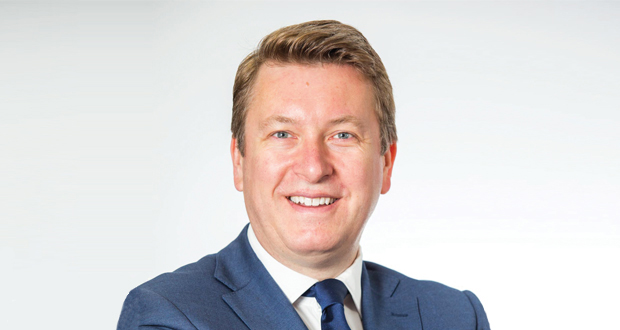
As an industry we’ve seen a lot of change over the last few years, particularly in the last 12 months as the move to home working triggered an explosion of digital services.
The world of building and development has been no different. Modern Methods of Construction (MMC) may already be a term familiar to some of us in the industry, and is set to be part of a new industrial revolution according to the government.
The term MMC encompasses approaches to housebuilding that are quicker and more efficient, and importantly where many of the components are fabricated offsite.
MMC might be a relatively new phenomenon in the UK, but countries around the globe have been benefitting from it for years.
Japan leads the way having first embraced MMC 50 years ago, Tokyo has the capacity to build more houses per year than the entire UK.
Elsewhere, Sweden is building at least 45% of new homes off-site in factories, China has set a target that 30% of all new buildings will be constructed off-site by 2026 and Singapore requires all development on government land to use modular construction.
So, with the UK failing to meet its 300,000 new homes a year target, MMC could be a critical part of solving the UK’s growing housing crisis. To that end the government has appointed an MMC champion, Mark Farmer, who has responsibility for developing the safety, quality and potential of the industry, which will be worth £40 billion a year once mature.
A recent report by Farmer recommended the government should set a target of 75,000 modular homes by 2030. The report says modular housing is ‘the biggest single gamechanger’ when it comes to adding to the country’s housing supply.
The government is also putting strong financial commitment behind MMC. To date more than £233 million of loans have been agreed for MMC projects by the government’s Home Building Fund.
And as part of the March Budget, the Ministry of Housing, Communities and Local Government announced plans to launch an MMC taskforce backed by £10 million of seed funding.
The government has also made MMC a condition of its strategic partnership grant programme, with all strategic partners expected to deliver a minimum of 25% of homes through MMC.
Alongside this, Homes England has also commissioned a significant research programme to evidence the impact of MMC within the housing sector across eight pilot sites, totalling approximately 1,800 homes.
It’s hoped that the evidence of the benefits of MMC use will provide greater confidence to the industry, investors, insurers and customers to support its use across the sector.
Why MMC?
The increased focus is understandable. MMC can deliver high-quality housing at pace and according to the government it has been shown that some homes built using MMC have 80% fewer defects and can reduce heating bills by up to 70%.
Some of the main benefits of MMC housing include:
- Speed: homes delivered using MMC are manufactured offsite with less disruption than onsite construction.
- Reduced carbon footprint: homes built using MMC have the potential to contribute significantly to the reduction of carbon emissions, through greater precision in the manufacturing process leading to more energy-efficient homes and reduced construction waste.
- Skills: production lines enable companies to take apprentices and train them on specific tasks irrespective of their backgrounds.
- Safety: As engineer and government building safety adviser Dame Judith Hackitt points out: “Over the longer term, it is expected that the changes set out in the report will lead to the greater use of more standard and better-quality assured systems being constructed offsite and less elemental construction onsite.”
Buyers should also not be concerned about quality as modular homes are built to last the same amount of time as a traditional property.
The new industrial revolution
It is in the North of England where the most exciting innovation in MMC is taking place, in a so-called ‘Northern Construction Corridor’ with digitally designed houses where the computer code feeds directly to the production floor, and the best automation and assembly-line production techniques.
This industrialisation of housebuilding offers a unique opportunity to drive affordability into the sector which can then, in turn, be passed on to the house buyer.
Economies of scale mean that the bigger the orders placed with modular businesses such as this, the better they are able to plan ahead and price competitively.
This means that in the long-term, MMC can be a large-scale solution for every tenure: social housing, home ownership, build to rent and market sale.
One unlikely advocate of MMC is financial services provider Legal & General (L&G) which has created its own modular homes business and factory in Sherburn, Yorkshire.
L&G has assembled a team of people with experience in sectors ranging from housebuilding and land development to aerospace and engineering.
Its latest project in Bristol will create 185 new homes in conjunction with the City’s council. Once the land has been cleared and prepared, the homes can be assembled on site within eight weeks.
The Bristol scheme will create some of the most energy efficient homes in the country with all homes achieving an energy performance certificate (EPC) standard A.
The combination of Air Source Heat Pumps, Photovoltaic Cells and high-quality build standards will put them in the top 1% for energy performance meaning significant energy savings for its residents. 50% of the homes will be delivered as affordable housing.
It’s clearly a growing business as Legal & General Modular Homes is currently looking to hire an additional 350 employees into the business this year.
And in a sign that the UK has started to make its presence felt on the world stage, Croydon becomes the proud home of the world’s tallest modular building this year, just 35 weeks after construction started.
The two towers of 101 George Street, developed by Tide and its sister company Vision Modular Systems in its Bedford factory, stand at 44-storeys and 135.6m. It is the tallest modular apartment tower in the world – the same height as the London Eye.
MMC will play a major role in the future of housebuilding. As an industry there is no reason to shy away from properties constructed in non-traditional ways. Close collaboration between lenders, developers and insurers is key to ensuring the success of these new style new homes.
Conveyancers should also make sure they are well informed about these new forms of buildings so they can properly advise clients on any implications.
Stephen Ward is director of strategy and external relations for the Council for Licensed Conveyancers (CLC)